DCW 2024 A Wates Project Manager reveals how he’s using AI on-site
Digital Construction Week is always a busy event for Buildots. And this year was no exception. Our long-term partner, Wates, joined us onstage to discuss its first-hand experiences using Buildots – and the associated productivity gains.
The Wates success story
So far, Buildots and Wates have embarked on 27 projects, covering more than 300,000 sqm (3,229,000 sqft) of construction surface.
One standout benefit of Buildots is how it streamlines trade management, said Wates Project Manager Tom Bell, who appeared onstage with Buildots product specialist Amir Berman. Tom explained that Buildots allows him to eliminate guesswork – and therefore conflict – from his role, “Subcontractor meetings can be difficult when it comes to assessing progress and opportunities. We all know those meetings mean lots of debating – ‘No, it’s your fault’ or ‘No, look at this drawing.’ Buildots helps navigate these conversations with credible and actionable insights.”
Cloudy with a chance of delays – introducing Delay Forecast
Buildots doesn’t just streamline trade collaboration and lower project managers’ blood pressure. By integrating AI with performance measurement, Wates also slashed delay risks. Using Buildots’ new Delay Forecast feature has been a major highlight for Wates. It predicts delay risks and alerts construction teams about pace issues, allowing them to stop delays in their tracks.
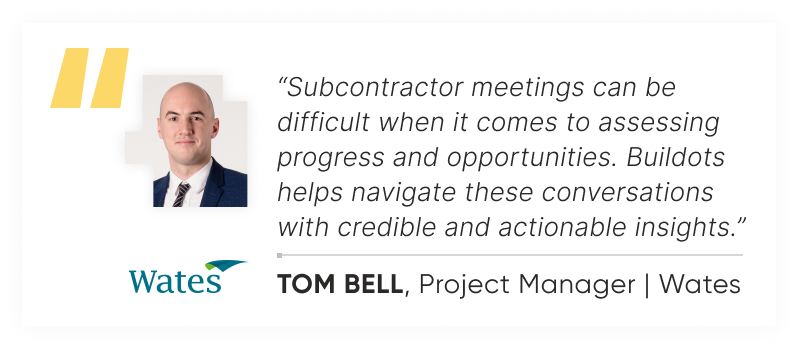
Consider this example. In March 2024, Buildots flagged that Wates could expect a six-week delay in installing lighting fittings on a project if the current pace continued. To craft a mitigation plan, Tom and his team first looked at areas of availability, clearly illustrated in the Buildots platform. Having ascertained that there were plenty of opportunities for work to continue, Tom analyzed the project’s historic pace and noticed that the planned pace of 72 fittings per week was consistently not being met. The Buildots platform told him he’d now need to hit a target of 114 weekly fittings to get back on track. Tom took this information to the relevant trade and agreed on a new strategy that reduced the projected delay to just one week. No finger-pointing. No blame game. Just practical solutions.
This is just one of many ways AI-captured data can optimize project timelines. It’s the ‘early warning system’ the construction industry desperately needs. Amir notes: “The real value of AI comes when you tie it into your day-to-day activities. That’s where it can help you be smarter, more efficient, and more precise in your decision-making. You don’t need to be super techy to embrace it.”
Performance Driven Construction Management – a new standard at Wates
How has Wates achieved such impressive results with AI? In short, by embracing Performance Driven Construction Management (PDCM). Developed by Buildots, the PDCM framework goes beyond traditional progress tracking. It focuses on measuring project performance using metrics like area utilization, pace and Percent Plan Complete (PPC).
PDCM relies on consistent data gathering (and therefore requires accurate and timely progress data). It transforms the classic management loop of ‘measure-analyze-optimize’ into a dynamic workflow that unlocks genuine continuous improvement. As the above example demonstrates, PDCM allows project teams to develop targeted risk mitigation plans to get projects back on track if something looks amiss.
We’re privileged to work with open-minded partners like Wates, who embrace the PDCM framework, new technology, and innovative approaches. As Tom explains, “The interface is very intuitive – with just a few clicks, you can deep-dive into a single activity, understanding how it's tracking against your program and its efficiency. The AI provides actionable insights very quickly”.
Keen to learn more? You can find other success stories from the field here.